PLE / SIL 3 BEHALEN MET 1 SCHAKELAAR
Are two safety switches required for PLe / SIL3?
There is a lot of interest in the question whether it is mandatory to use 2 safety switches for PLe applications.
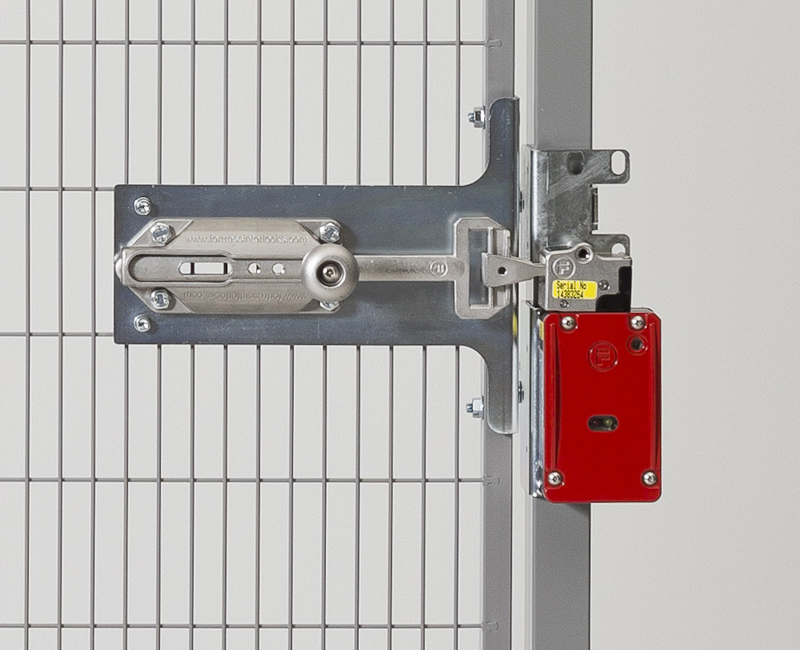
This discussion has been going on for years but has only really come to the attention since a note was added to table D8 of the ISO 13489-2-2012 in 2012:
‘ For PLe a fault exclusion for mechanical (e. g. the mechanical link between actuator and contact element) and electrical aspects is not allowed. In this case redundancy is necessary’
Two paragraphs from the recently published EN ISO 14119 (the interlocks standard) give a slightly different view of the topics “Assessment of faults” and “Fault exclusions.” Where an interlock system requires PLr e……… In order to achieve this it is normally not justifiable to exclude faults, such as broken actuators. '
‘There should be a proper selection of the device ensuring that the holding force (Fzh – see 5.7.4) of the guard locking device is sufficient…….. In this case the use of fault exclusion for breakage of the locking element does not necessarily limit the PL or SIL for the guard locking function.’
What does this mean in practice?
It is clear that the above-mentioned standards have different views on whether or not to apply fault exclusions. Where in the first example there is still talk of “not allowed”, this changes in the second and third examples from “normally not justifiable” to “does not have to be a limiting factor”. Nevertheless, the common message is: The breaking of tongues / keys (hereinafter referred to as “actuators”) should be included in the assessment in PLe applications.
This is understandable when using standard safety switches, as it is not uncommon for actuators to break down, resulting in a fail-to-danger situation.
The design of the Fortress amGard Pro head modules and actuators was the starting point to create an indestructible solution that meets the interlocks standard. By producing all force-bearing components from oversized stainless steel, Fortress Interlocks has developed an actuator that can absorb more than 50x the energy than a standard actuator and a head module that can withstand more than 4,000KG of pulling force. The result is a safety switch that is stronger than the door and the hinges on which it is mounted.
The oversizing, extensive testing and the data of more than 3 billion hours of in-use products give Fortress Interlocks and TÜV SÜD the proof that one amGard Pro is a PLe safety switch and that a second safety switch is not necessary.
Conclusion
For PLe applications, the actuator needs attention. If you use a standard actuator, even for light-duty applications, you have to use a second safety switch. It is also possible to use a safety switch in combination with a non-contact switch (safety sensor). However, it is easier to achieve PLe if one Fortress Interlocks amGard Pro switch is used (i.e. with a head module and tongue that are stronger than the shield itself).
Oversizing creates mechanical fault exclusion
1 amGard Pro switch achieves PLe
We are
here to help
Contact one of our technical specialists or sales engineers
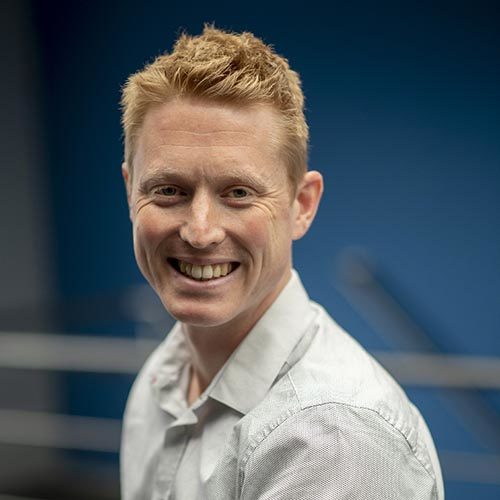
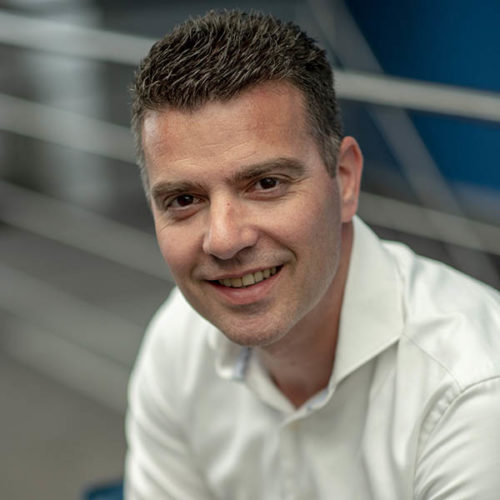
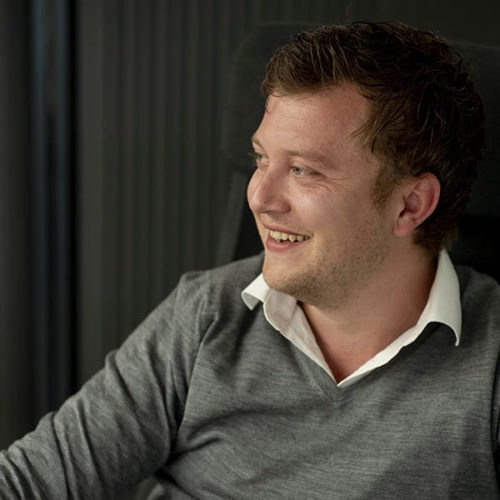
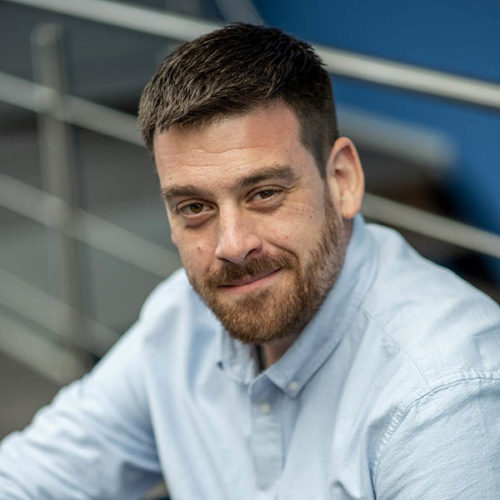
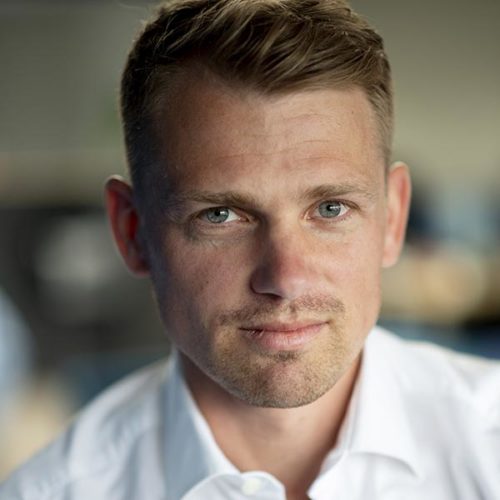
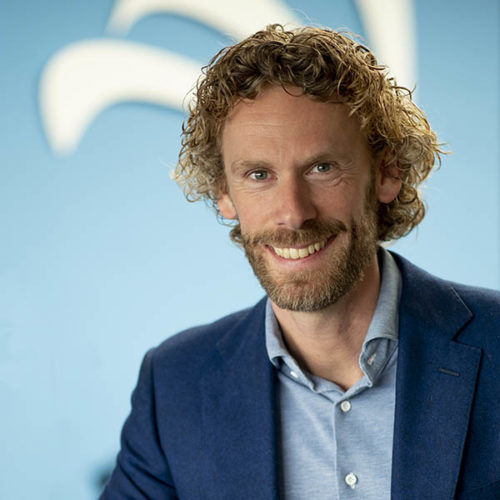
Request
a meeting
For all your questions about our products and services, please fill in the form below (response within 1 working day).