MACHINE SAFETY AT VDL NEDCAR
550 Safety switches and kilometers of machine guarding
In the autumn of 2016, we walk into the renovated factory of VDL Nedcar. At the entrance, we see a Mini from the year 1959 complete with original details. VDL Nedcar is the only car manufacturer of series models in the Netherlands and the pay a lot of attention to safety.
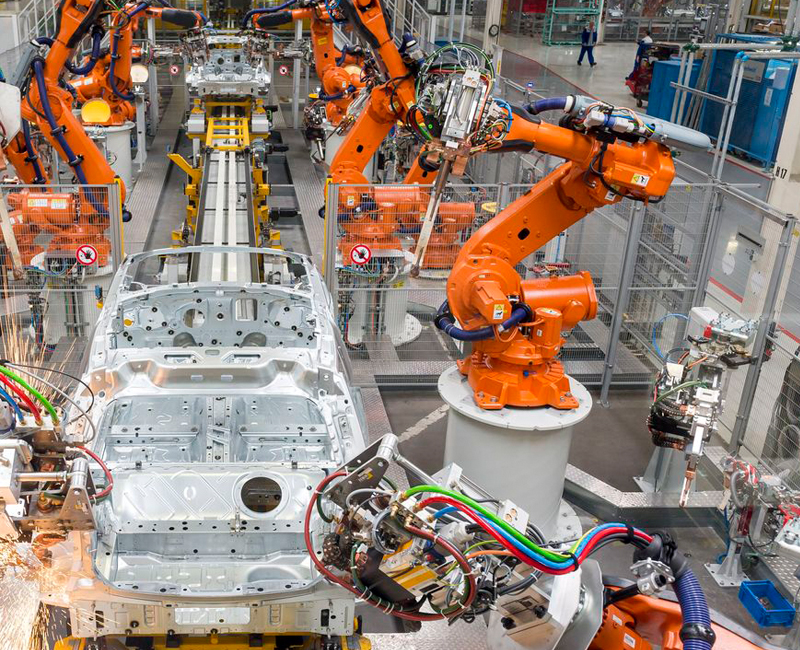
The company is located in Born, Limburg, and is highly automated and equipped with an impressive number of robots. USP and VDL Nedcar are working together to bring safety within the factory to the highest level. With innovative solutions in the field of machine guarding and access control to these protected areas, potentially risky situations are prevented. This with minimal disruption to production.
A look behind the scenes at VDL Nedcar
Nedcar was founded in 1967 by DAF as a passenger car factory. At the beginning of July 2012, it was announced that the Eindhoven VDL Group, founded by Mr. Van Der Leegte, wanted to take over the Nedcar company. VDL Nedcar now has 5,500 employees.
We are welcomed with Limburg hospitality by Peter Schusser, Maintenance Engineer at VDL Nedcar, who guides us through the building and the factory. This is part of the safety policy. The imposing factory consists of a Press Shop, the Bodyshop (body shop), the Paintshop and the Final assembly. It takes at least half an hour to get from one side to the other side of the factory. Large TV screens are installed at various locations in the production halls. These follow the behaviour of the production line and indicate whether the line is behind or ahead of production. At the Bodyshop, automation is 98%. The paint shop (Paintshop) is also highly automated. In the assembly department, there is less automation because adding small particles on the assembly line is a human effort and requires more precision.
The need for machine safety in a factory full of robots
The factory has 1200 robots that perform large parts of work in the VDL Nedcar factory. The robots work almost autonomously after they have been correctly programmed. A crane automatically removes the body from the highest levels of the shelves, cameras detect where the holes of the hinges are in the body and also do the measuring. The robot can choose its tools but with limited control. There are also parts in the process where two robots work in synchronization on one bodywork. The strongest robots can carry up to 600 kilos. They are very efficient these robots, but also exciting when you walk into a cell for the first time. Only then does one really realize the importance of machine safety to protect an employee.
VDL Nedcar influences safe behaviour in the workplace with compulsory courses. This is a condition to be allowed to work with the machines. All procedures are also recorded in specific instructions and manuals. Colleagues also keep each other sharp and work according to ISO guidelines. More importantly, the entire factory is equipped with machine safety products supplied by USP. Think of machine guards and safety fences from Troax, safety switches from Fortress Interlocks and safety padlocks from Masterlock. VDL Nedcar has been using safety switches from Fortress Interlocks for over 20 years. Unique Safety Products has been the exclusive supplier of Fortress in the Netherlands since 2010.
How does a safety switch work in practice?
Step 1: The employee submits a request for unlocking via the blue illuminated push button.
Step 2: When the machine is stopped and safe, the switch is released.
Step 3: Only employees with an access key can open the door (line managers and maintenance personnel).
Step 4: After inserting and turning the access key, the safety key is released. These have to be taken into the guarded area to prevent personal containment.
Step 5: After the work has been completed, the door gets closed, the safety key gets entered and turned, then the access key gets turned and can be removed, the installation is reset using the yellow and white illuminated push buttons. Peter Schusser experiences a safety key as a personal security guarantee. Peter has 35 years of experience within VDL Nedcar and is close to the people. He is almost always on the floor, so he is also quickly on-site if there is a fault. Peter clearly has a passion for his work.
Access keys for authorized access
Access request and reset at the entrance door
Wij staan
voor u klaar
Neem direct contact op met één van onze specialisten of sales engineers.
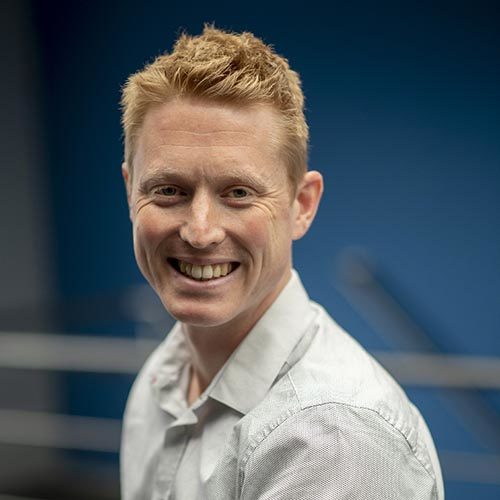
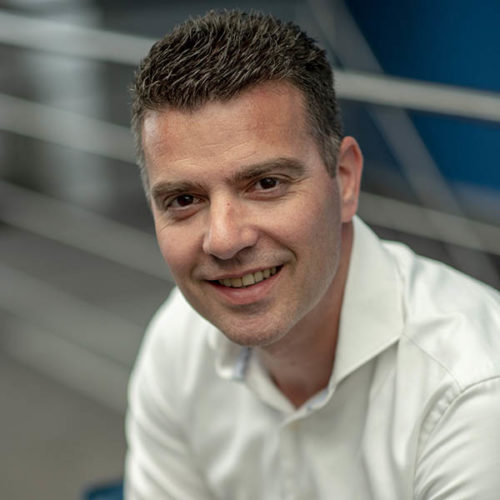
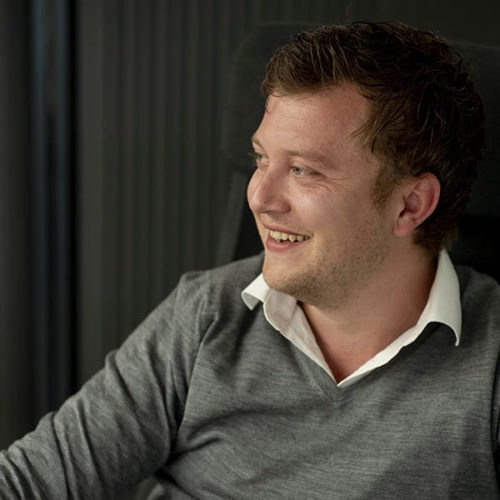
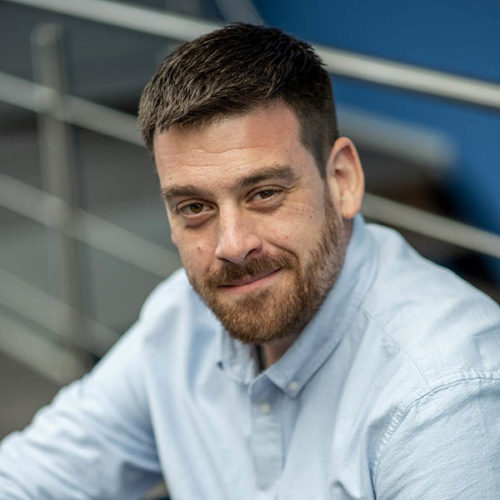
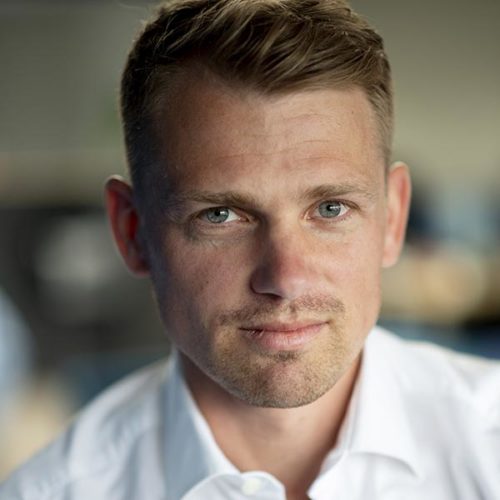
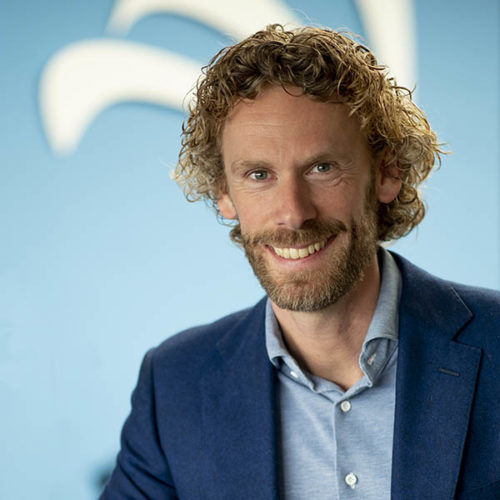
Vrijblijvend
adviesgesprek
Voor al uw vragen over onze producten en diensten kunt u onderstaand formulier invullen (reactie binnen 1 werkdag).